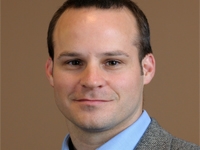
Direct-Drive Wind Turbines: Can the Chinese Keep Their Lead?
By Andy WicklessChinese wind turbine manufacturers have experienced explosive growth in recent years. Sinovel, which installed its first wind turbine in 2006, was ranked as the world’s second largest wind turbine manufacturer in 2010 – ahead of companies like GE, Gamesa, and Siemens. In 2010, four of the top ten original equipment manufacturers (OEMs) were Chinese.
Most of the increase in market share of Chinese OEMs is due to the strong domestic market. Driven by aggressive government targets and domestic manufacturing policies, China increased its share of the global wind market from 22 percent in 2008 to 48 percent in 2010.
Through strategic acquisitions, some Chinese OEMs have quickly gained access to formidable R&D capabilities, particularly in the area of direct-drive technology. While two of the top three direct-drive turbine manufacturers in 2010 were Chinese, global power leaders like GE and Siemens are rapidly testing and deploying gearless turbines of their own.
Whether Chinese OEMs can maintain their position as leaders in the growing direct-drive segment will depend primarily on potential supply chain constraints for critical components and renewable energy targets set by the Chinese government.
Direct-drive segment shows strong growth
Since the infancy of the modern wind industry, geared wind turbines have been the industry’s standard design. Direct-drive turbines, however, are gaining market share.
According to The World Market Update 2010, published by BTM Consult–a part of Navigant, direct-drive turbines comprised approximately 12 percent of the world’s total number of turbines in 2008, on a megawatt basis. By 2010, the share had increased to approximately 18 percent. The World Market Update 2010 estimates that this percentage could continue to rise to 20-25 percent by 2016.
The main driver behind increased demand for direct-drive turbines is the risk of gearbox failure. Gearbox problems have been an ongoing and major issue for the wind industry. When a gearbox malfunctions, wind farm owners can incur hundreds of thousands of U.S. dollars in increased maintenance costs, crane rental costs, and lost power sales, depending on the warranty and insurance policies they have in place.
Direct-drive turbines eliminate the need for a gearbox all together by directly connecting the rotor to the generator. This lack of gearbox failure is particularly attractive in offshore applications since accessing turbines offshore can be much more difficult given the more challenging marine weather and the need to secure appropriate vessels in a timely manner. Weather delays offshore can also significantly increase maintenance costs and lost power sales, relative to onshore costs.
With their simpler design and fewer components, direct-drive turbines may seem like a logical offshore choice, but they also have their drawbacks. Direct-drive turbines are largely unproven in the offshore environment on a commercial scale. Their operating history is significantly less than that of geared turbines.
As a result, financiers are wary of the perceived added technology risk. Another issue is the added cost of producing and installing direct-drive machines due to their larger dimensions and heavier top head mass. In offshore applications, larger vessels and cranes are needed, but have historically been in relatively short supply.
Chinese OEMs move out in front
Enercon, the long-time market leader in direct-drive turbines, lost its lead on an annual basis in 2010 to Chinese manufacturer Goldwind. Another Chinese OEM, XEMC Darwind, is now comfortably in third place. While Chinese OEMs comprised just 3 percent of the global market for direct-drive turbines in 2008, they accounted for more than 50 percent in 2010.
In 2004, Goldwind began licensing gearless turbine technology from Vensys, a German design company not involved in turbine manufacturing at the time. In 2008, Goldwind purchased 70 percent of Vensys, gaining greater control over the direction of R&D and easing constraints on access to intellectual property.
XEMC Windpower originally acquired direct-drive technology from Zephyros, and subsequently increased its gearless turbine capability in 2009 by acquiring Dutch direct-drive technology specialist Darwind, beating out offers from competitors such as Alstom and Hyundai.
The West challenges
Chinese OEMs are not alone in their pursuit of direct-drive technology. Global powerhouses GE and Siemens are also developing gearless turbines. Like Goldwind and XEMC Windpower, GE gained access to direct drive technology via acquisition—acquiring Norway-based Scanwind in 2009.
While Vestas and Siemens have dominated the offshore turbine market to date, GE, the world’s third largest turbine supplier in 2010, has been notably absent since developing the Arklow Bank project in Ireland in 2004. GE views the Scanwind acquisition, however, as its ticket to re-enter the offshore market.
While Siemens’ strong position in the offshore market has been based to date on geared turbines, the company has been strongly pursuing the development of direct drive turbines since 2008 when it installed its first 3.6 MW direct-drive prototype in Denmark.
While the Chinese OEMs have reason to worry about the progress made by GE and Siemens in direct-drive technology, they may not need to worry as much (for now) about Vestas, the world’s largest wind turbine supplier.
Although many OEMs are betting on direct-drive turbines being the preferred design in the offshore market, Vestas isn’t convinced. Vestas’ President of Technology R&D, Finn Strom Madsen, has stated, “We are able to design direct-drive solutions, but they are less attractive because they provide a poorer business case for our customers."[1] In designing its 7 MW offshore turbine, Vestas ran two parallel R&D tracks, one each for geared and gearless designs—with the proven gearbox technology winning out.
Supply chain concerns loom
All of the emerging direct-drive concepts on the market include permanent magnet generators. While it may not be immediately evident, this could serve as a competitive advantage for Chinese OEMs, at least in the near term. In 2010, the Chinese mining industry accounted for more than 95 percent of the global supply of rare earth metals, including neodymium, a rare earth metal and the preferred material for permanent magnets.
In recent years, however, China has restricted exports of rare earth elements such as neodymium. If China were to produce only enough neodymium to meet the demand of its domestic industries, it could seriously jeopardize the direct-drive turbine efforts of non-Chinese OEMs. Thus, the World Trade Organization is reviewing China’s raw material export quotas amidst pressure from both the U.S. and the European Union.
In June 2011, Chinese OEM Mingyang announced that it had been granted priority access to rare earth metals by the government of Ganzhou. Mingyang was given the right to be a leading investor in the Ganzhou Rare Earth Mineral Industry Group, a state-owned company with rare earth resource development rights in eight counties.
In the near-term, government-directed export policies and the type of strategic partnership entered into by Mingyang could position Chinese OEMs very well in the direct-drive turbine segment.
In the longer-term, however, neodymium supply constraints are likely to be less of a concern for non-Chinese OEMs. While neodymium is classified as a rare earth metal, it is no rarer than copper. It is widely distributed in the earth’s crust.
Until now, China has been the principal supplier of neodymium, but other mineral-rich countries such as the U.S., South Africa, Australia, and Brazil could begin to actively mine the metal in the face of supply constraints. In fact, in early July 2011, Siemens signed a letter of intent with Australian mining company Lynas to form a joint venture for the production of neodymium-based permanent magnets.
The CEO of Siemens' Drive Technologies Division noted, "This planned joint venture has strategic importance for us to secure a long-term and stable supply with high-performance magnets."[2]
In addition to securing supplies of rare earth metals outside of China, turbine manufacturers are also researching direct-drive turbine designs that do not require rare earth metal-based permanent magnets.
In July 2011, the U.S. Department of Energy awarded grants to six American-based projects to advance next-generation designs for wind turbine drive trains. Some of the grant recipients are now working on designs that reduce or completely eliminate the need for rare earth materials.
Geographic silos…for now
Because market share in the wind industry is typically expressed in terms of the global market, this masks the geographic-specific nature of competition. For all intents and purposes, the Chinese wind market belongs to the Chinese OEMs. Similarly, the North American and European wind markets are dominated by non-Chinese OEMs.
While only 28 percent of turbines sold in the Chinese market in 2005 were manufactured by domestic OEMs, by 2010 the share had grown dramatically to 90 percent. Foreign suppliers find it very difficult to compete in the Chinese market due to falling market prices and strict domestic content rules, although the latter have recently been relaxed.
While non-Chinese manufacturers have found relatively little traction in the Chinese market, they have not had to compete with Chinese OEMs in the North American and European markets. In a global wind market of 39,404 MW in 2010, Chinese OEMs exported less than 20 MW of turbines – next to nothing.
Given the long transmission interconnection queues in China and rapidly expanding turbine production capacity among Chinese OEMs, these OEMs will be looking for new markets to sell their turbines. Recently, Goldwind did what many of its predecessors have done to secure a market for its turbines—it acquired a wind farm under development to install its own turbines.
In December 2010, Goldwind acquired the 109 MW Shady Oaks project in the U.S. state of Illinois with plans to use 71 of its 1.5 MW permanent magnet direct-drive turbines. In the near-term, North American and European financiers are unlikely to finance many projects using Chinese-made turbines, given the lack of operating history compared to those made by OEMs such as Vestas, Siemens, and GE.
While Chinese OEMs can follow the self-financing strategy used by Goldwind, this is unlikely to be a sustainable strategy over the long term given the capital outlays involved. If Chinese OEMs, however, can install enough turbines in markets outside of China to sufficiently demonstrate reliable performance to banks, they may begin to challenge western OEMs in their home markets, much like Chinese solar panel manufacturers have done.
Conclusions
The demand for direct drive wind turbines is on the rise due to concerns about gearbox reliability, especially as the offshore market is growing rapidly.
In just a few short years, Chinese OEMs (primarily Goldwind and XEMC Darwind) have positioned themselves as leaders in the direct-drive segment. Industry veterans such as GE and Siemens, however, are looking to quickly catch up. If direct-drive turbines become a major portion of the overall turbine market, Chinese OEMs could end up with an even greater percentage of the global wind market than they have today.
[1] https://www.reuters.com/article/2011/03/30/us-vestas-idUSTRE72T4TH20110330
[2] https://www.siemens.com/press/en/pressrelease/?press=/en/pressrelease/2011/industry/i20110742.htm